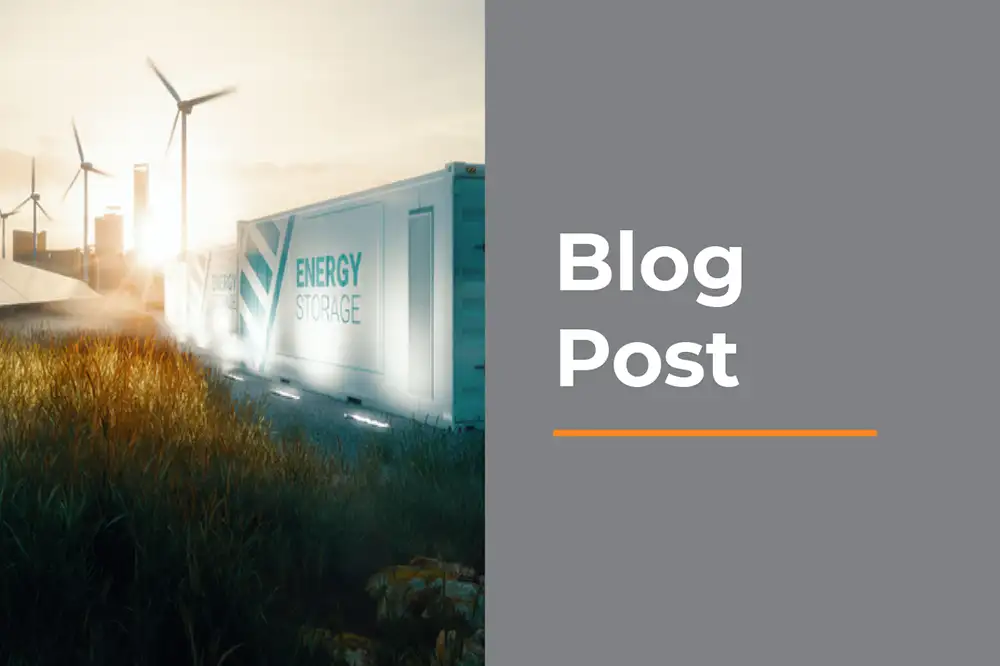
Charged Choices: The LFP VS NMC Question
The industry has homed in on lithium ion batteries as the main battery used in storage. Recently, the terms NMC and LFP have been popping up everywhere, as the two different types of batteries vie for prominence. Joonki Song, our Senior Director of Marketing and Supply Chain, explains the different solutions and their pros and cons.
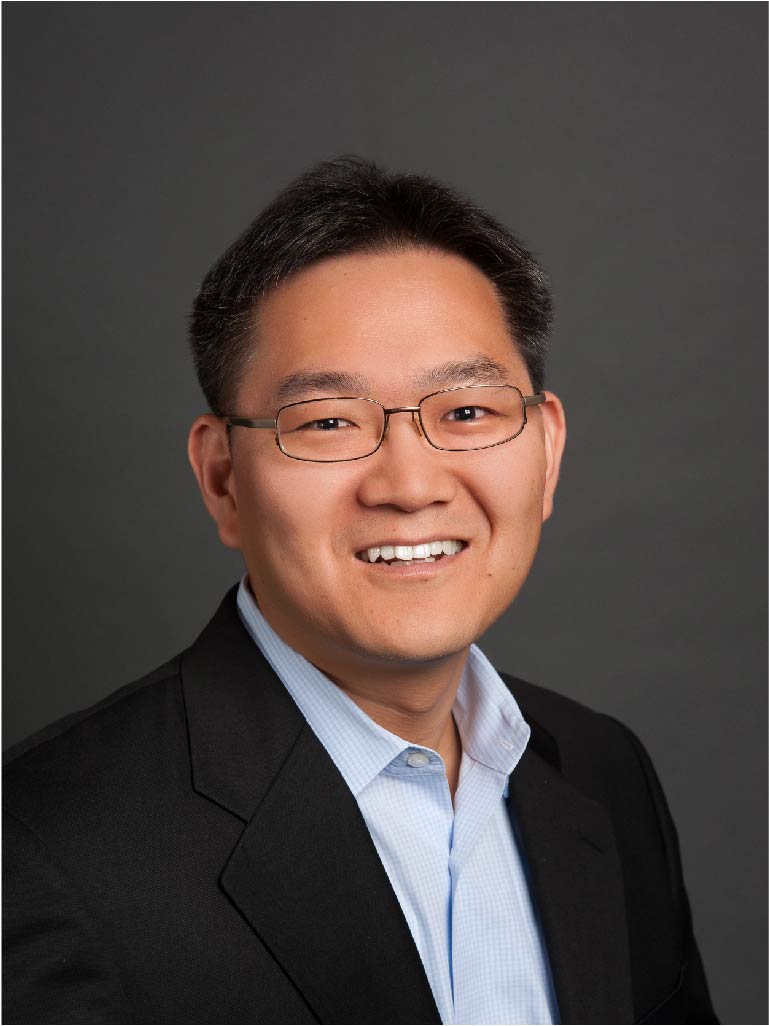
By: Joonki Song, Senior Director of Marketing and Supply Chain
The NMC vs LFP question
These are not new technologies that are different from Li-ion batteries. Actually, LFP and NMC are two different sub-chemistries under Li-Ion batteries. LFP uses Lithium-phosphate as cathode material. NMC uses Lithium, Manganese, and Cobalt as cathode material. IHI Terrasun has been procuring both NMC batteries and LFP batteries.
To understand why people are talking so much about both technologies, we can look at Terrasun’s procurement story. In the US energy storage industry, until maybe two years ago or so, most of the projects were deployed with NMC Li-Ion batteries. Samsung SDI and LGChem have been the dominant battery suppliers, and we were leveraging those suppliers as well. I am not so sure why LFP batteries were not being deployed much in the US at that time. In 2018 there was big global ESS market growth, over 2X growth from 2017 roughly from 2GWh to over 4GWh, and half of the demand came from the South Korean market due to their lucrative renewable and energy storage incentives. Suddenly, the battery supplies from these two major companies whose HQs are based in South Korea, were not enough for the US market and not for Terrasun.
So we had to find a new way to support our customers. We started reaching out to reputable LFP battery companies. LFP batteries have been produced for a long time, but the batteries were mainly manufactured and consumed in China for electric buses and other applications. Now, with some meaningful deployments of LFP batteries in the US, more and more companies seem familiar with the LFP batteries and the companies who produce them. I think this story can resonate with many people in the industry.
Understanding the differences between LFP and NMC
Typically, NMC is known for high energy density, which means there will be more energy with the same amount of battery. From our perspective when we integrate hardware and software for our projects, this difference impacts our enclosure design and cost. Depending on different batteries, I would say our enclosure cost (structure, cooling, safety, electrical BOS components, etc.) is about 1.2- 1.5X higher with LFP than NMC. LFP is known as more stable chemistry, which means the temperature threshold for thermal runaway (or fire) is higher than that of NCM. We saw this ourselves when testing the batteries for UL9540a certification. But there are also many similarities between LFP and NMC. The round-trip efficiencies are similar, and so are the common factors that impact battery performance such as temperature and C rate (how fast you charge or discharge).
So why would you choose one over the other?
In addition to the technical differences that are coming from cell chemistry difference, there are other differences like operational conditions, pricing, other commercial terms, approach toward the payment terms, and more. Some of them are coming from the fact that the companies have different experiences and are in different developmental stages rather than the technology difference itself.
Commercially, LFP batteries’ initial capex pricing is typically more competitive than that of NMC. I am generalizing here. LFP is around 20-30% cheaper on $/KWh, but total system beginning of life system integration cost tends to only be around 5-15% cheaper. End of life (EOL) based capex is more complex to compare. It really needs to be assessed product by product or even project by project on their cycling & calendar performance, warranty/guarantee, ease of augmentation, etc. – no clear answers.
Operationally, we like the looser operational conditions from LFP – wider temperature range than NMC, no requirement of reefer container while shipping. Also, typically LFP battery products support up to 1C operation whereas in NMC you must use the power battery, a different batteries from 2H or 4H use batteries, to support 1C rate (1 hour) application, which costs more. LFP batteries degrade much faster in the first six months. This can create confusion and issues if the projects are large and need to be delivered/commissioned over couple of months because the first shipped batteries could degrade to, for example, 98% or 96% of state of health by the time the last batches are commissioned.
We think that NMC products and companies are better perceived by the customers and investors still, which is important to recognize. But leading LFP batteries and companies have been catching up. And once a product is approved, customers typically have no problem adopting new platforms from the same company.
The industry is moving towards balance.
There are pros and cons to both LFP and NMC, and we use both! We select the batteries and other major components based on 7 criteria. Those are company, price, other commercials, product fit, project management, consistency of supply, and services. Obviously, pricing is very important. But we consider product integration fit and safety very seriously. Recently, warranty and consistency of supply have become more important to us.
So, in that sense, we really do not think about LFP or NMC as any kind of criteria. We try to understand the differences and value the best aspects of each technology.
As a technology adopter, we are very excited to see these two technologies competing each other. It will promote healthy growth in the industry, which is good news for the customers. My sense is that most ESS customers would be willing to consume both technologies. They will choose one or the other not because of their technical differences but based on the overall lifecycle costs, and they will continue to make decisions as new technologies come into the market as the industry continuously advances.
Read more: