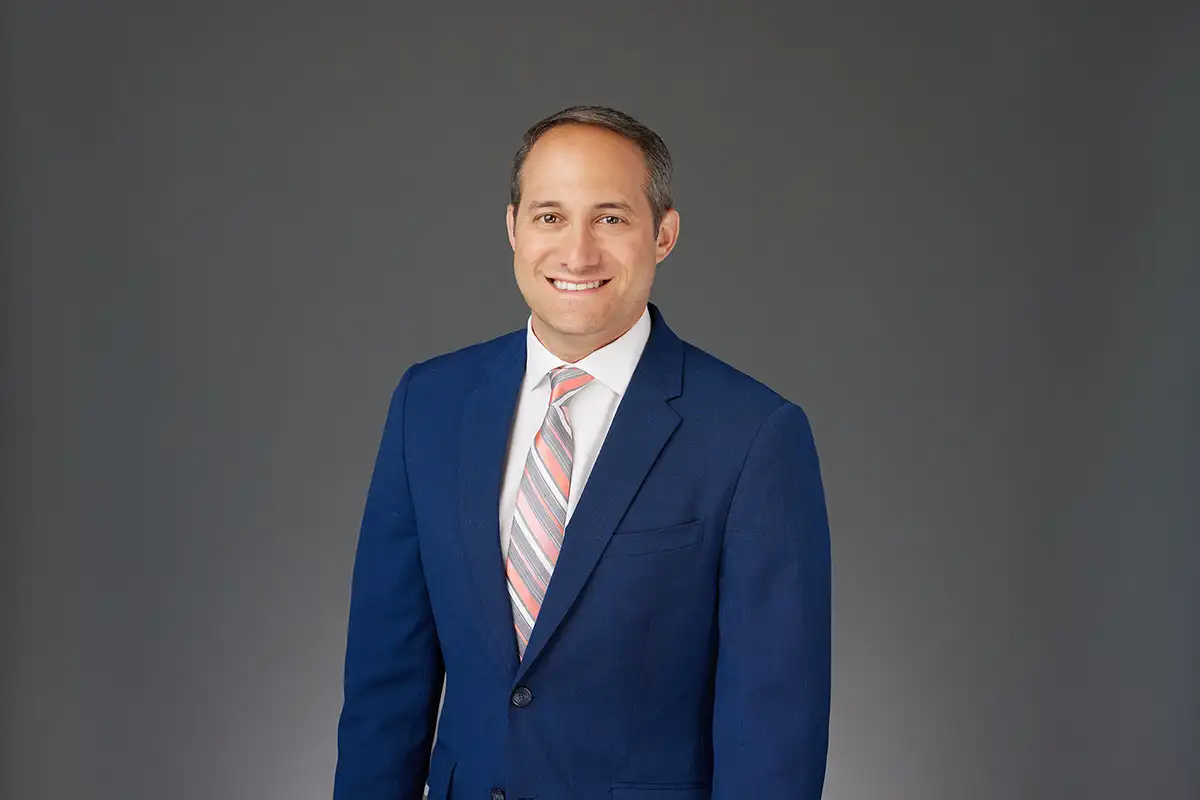
Webinar: What You Need to Know About UL9540 Codes and Standards for Battery Storage
Battery manufacturers come up with new products roughly every two years. But as each new product comes to market, energy storage systems integrators must perform a detailed vetting process that includes all codes to ensure compliance before starting any project.
Codes and standards define operations of much of the modern world and clean energy systems are no exception. Codes and standards in renewable energy are especially critical since they are written to ensure safety. As experts in energy storage integration and safety, IHI Terrasun organized a webinar about developments in UL9540 codes and standards for battery storage. We invited Dr. Carrie Kaplan and Dr. Mark Kellenberger from DNV and Steve Douglas from QPS to join us, with Andy Colthorpe, Editor of Energy Storage News, serving as moderator.
Codes and standards always play a vital role in the journey to bankability and maturity in the industry.
Energy storage shares similarities with the solar photovoltaic (PV) industry, in that both are relative newcomers to the energy sector. The energy storage industry is earlier in its development, however, it’s clear that standards helped solar PV gradually become a bankable set of technologies for investors and now developing and refining these standards will also ensure a faster adoption of battery energy storage worldwide.
Clean technology cannot establish itself as a vital piece of global energy market without public confidence in its safety and the illustrated long-term reliability needed for the financial sector to invest in its development. This explains the need for UL9540: including its importance to an integrator of battery systems; what a system integrator must do to make sure any project is compliant; how to document that a system will meet all the codes and safety requirements; and why a developer should interface early and frequently with local authorities.
What is UL9540 and why is it important?
UL9540 is a required safety listing and certification for energy storage systems (ESS) that provides a comprehensive roadmap for ensuring their safe and reliable operation. The standard sets rigorous requirements for the design, construction, testing, and operation of ESS.
Currently, UL9540 is in its second revision; the first edition of the standard was issued in 2016. A technical panel of 120+ members (of which Larry Kane from IHI Terrasun and Steve Douglas from QPS are members) makes recommendations and changes to help the standard develop, evolve, and become safer for all participants. These members come from across the country and include energy storage manufacturers, testing labs, energy storage systems integrators, and utilities.
UL9540 ensures that battery energy storage systems meet the major electrical safety codes for site safety and personnel safety. Those include NFPA 70, which is the National Electric Code, and NFPA 855, which is the standard for the installation of stationary energy storage systems. NFPA 855 has now become the nationally accepted code that local and state jurisdictions reference when defining project requirements. UL9540 can be applied specifically to battery cabinets or be used to include the inverters and DC/DC converters for systems that are either AC-coupled or DC-coupled.
When working on projects as an energy storage systems integrator, for UL9540 compliance it's important to review all the safety features that will allow that system to operate properly and protect life safety, land safety, and personnel. A safety analysis must be created which includes a hazards mitigation analysis and a failure modes effects analysis.
When the engineering team at IHI Terrasun creates these documents, they follow military standards1629-Alpha (MIL-STD-1629A). Safety analyses include thorough and detailed descriptions of the power plant control system, along with its features and functions. In addition, all sub-components of the system are documented, ensuring that they have either been tested individually by a national lab or they are tested as part of the UL9540 field evaluation. Documentation of critical failure modes and causes is used to be able to prove to Authorities Having Jurisdiction (AHJs) that the system will perform safely.
Scrupulous Documentation Is Key
The chart below is an example of documentation of the sub-components of the fire suppression system inverters, each of which will typically have their own UL listings. For example, in item #4, a unique DC disconnect was tested by QPS in the field as part of the UL9540 field evaluation.
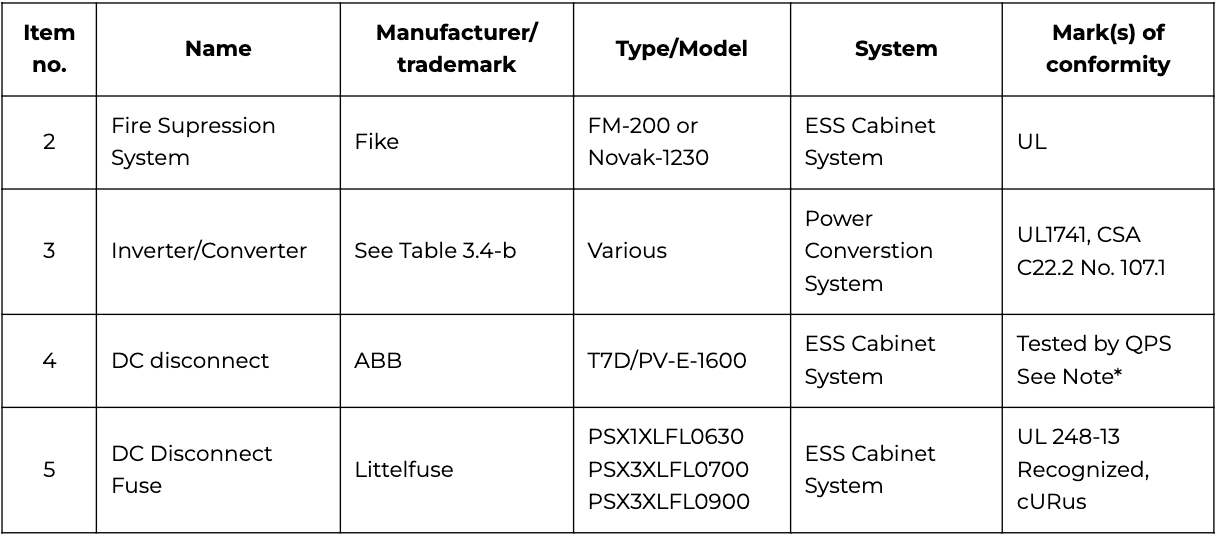
Critical failure modes also need to be identified by the system integrator to ensure that the battery storage system, the associated inverters or DC/DC converters, and the safety functions are thoroughly evaluated. Category I failures are catastrophic and can cause death; Category II failures are critical and could lead to injury or major property damage.
Each component has to be evaluated as to how it could fail, what measures are in place to prevent failure, and what critical components have been designed and tested for mitigation.
The short circuit pathways and protective devices must be considered, along with every component in the system, including the batteries, inverters and any cooling systems, such as air-cooled HVAC units or chillers.
Finally, a failure modes effects analysis worksheet is created that details all the components of the system. The document below shows just the high-level items that are included for battery systems or power conversion systems. Within each category, all of the various components are documented, as well as their severity class and how they could fail and how that failure is mitigated.
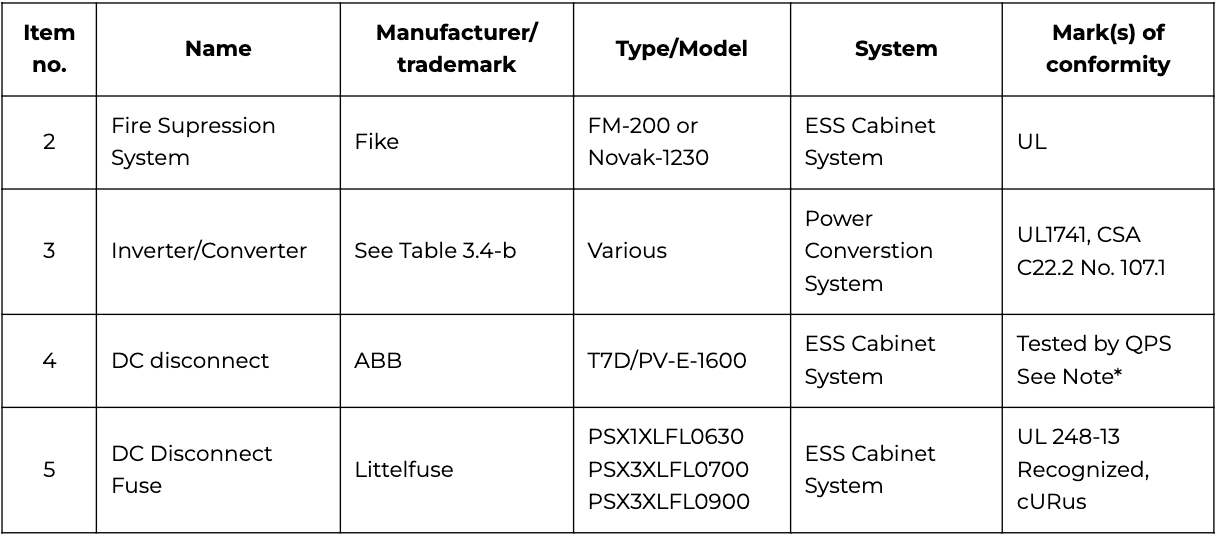
What Do the New Code Changes Require?
The biggest recent change to codes was in 2021 with NFPA 855, which now requires battery cabinets to meet either NFPA 68 or NFPA 69 standards. NFPA 68 focuses on deflagration venting and NFPA 69 focuses on explosion prevention venting. Previously, it was not specifically stated that energy storage cabinets had to meet these standards. Now, however, a gas detection system must be provided with 24 hours of standby power and two hours of power in an alarm state.
Going forward, these changes to the code, with requirements for an additional detection system, will need to be considered by both energy storage systems integrators and developers. Performing a detailed computational fluid dynamics (CFD) analysis of the full battery cabinet should be considered. This should include an analysis of how gas enters the system in a failed state to prove that the gas removal mechanisms will keep the system safe and below the flammability and explosive limits allowed by the code. Another update to note is that with the 2023 edition of NFPA 855, smoke and fire detection systems also must have similar 24-hour standby power and two hours in alarm, and they need to be in accordance with NFPA 72.
Battery manufacturers come up with new products roughly every two years. But as each new product comes to market, battery energy storage system integrators must perform a detailed vetting process that includes all codes to ensure compliance before starting any project. Failure to do so can result in delays to permitting and the ability to operate the site.
Battery energy storage system integrators have to work with the developer and the local authority having jurisdiction (AHJ) of the site to ensure that not only NFPA 855 and UL9540 requirements, but also local codes and any individual requirements for that site, are provided. Going through this process means that all parties involved better understand how all the individual components work and how to build a compliant and comprehensive system around them.
Whether we integrate standalone battery energy storage projects or develop sites that are AC-coupled or DC-coupled with solar, the focus remains on the battery and the inverter. If the products used for the battery cabinet and the inverters go through their individual testing, IHI Terrasun's team can ensure overall safety — and meet the customers' specific project needs.